Ratholing is a common challenge in the storage and handling of bulk materials. If not prevented, this issue can lead to uneven flow, wasted space, and operational inefficiencies. Fortunately, there are ways to prevent ratholing through proper design, maintenance, and flow aids.
What Is Ratholing?
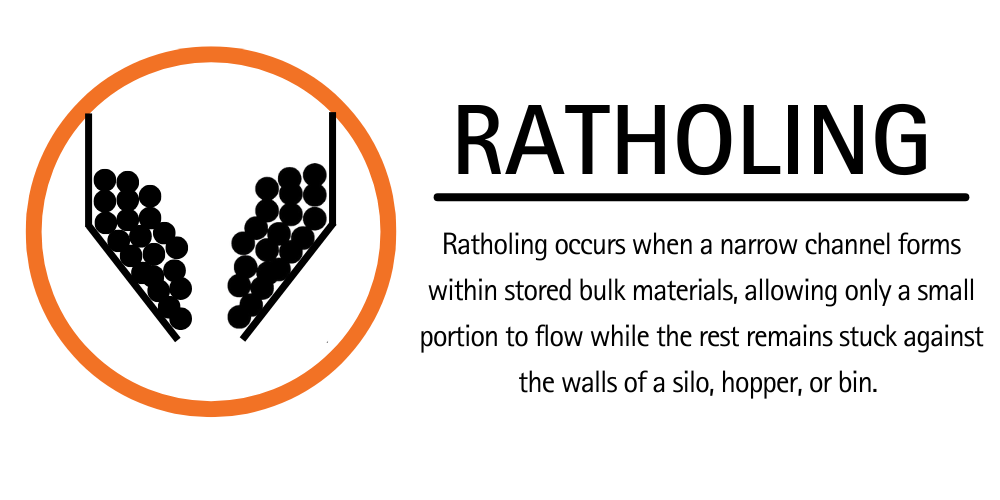
Ratholing happens when material only flows through a narrow channel, leaving large portions stuck around the edges of a storage structure like a silo or hopper.
The result? Materials remain trapped, reducing the overall storage capacity and making it harder to empty the bin or silo effectively.
Materials Prone to Ratholing
Ratholing typically occurs with materials that have poor flow characteristics, often due to their cohesiveness, fine particle size, or moisture content.
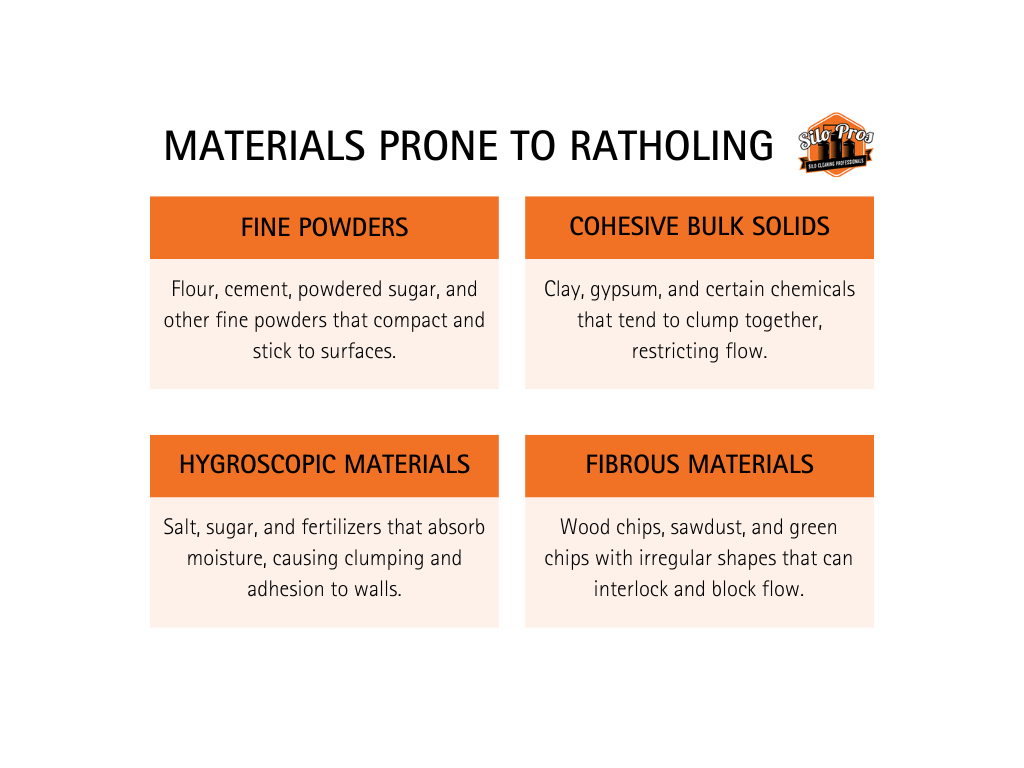
Common materials that are prone to causing ratholing include:
- Fine Powders: Materials like flour, cement, powdered sugar, and other fine powders tend to compact and stick to the sides of silos or hoppers.
- Cohesive Bulk Solids: Materials like clay, gypsum, and certain types of chemicals that have a tendency to stick together can create ratholing. These materials can form clumps or bonds that restrict flow.
- Moist or Hygroscopic Materials: Substances that absorb moisture from the air, like salt, sugar, or fertilizers, can clump together, leading to ratholing. The moisture can cause the material to adhere to the silo or hopper walls.
- Fibrous or Granular Materials: Materials like wood chips, sawdust, or green chips can create ratholing due to their irregular shapes, which may interlock and form blockages in the flow path.
What is the importance of preventing ratholing?
#1 It can disrupt operations. When a silo can’t empty properly, it means more time and effort are needed for cleanouts, leading to costly downtime.
#2 Stuck material can degrade over time, which affects product quality. Avoiding ratholing keeps your process efficient and your products in top shape.
Storage Structure Design Strategies for Preventing Ratholing
One of the best ways to prevent ratholing is to design storage structures that promote consistent flow.
Here are a few key strategies:
Design for Mass Flow
Mass flow means that all material moves together, without any stagnant zones. It contrasts with funnel flow, where material flows through a narrow path while the rest remains stationary. To achieve mass flow, the design of your silo or hopper is crucial. For example, ensuring that the hopper outlet is wide enough and has a steep enough slope can help prevent material from getting stuck. When the angle of the hopper walls is too shallow, bulk solids like fine powder tend to stick and form rat holes.
Choose the Right Flow Aids
Flow aids can make a big difference. Bin activators, screw feeders, pneumatic vibrators, and acoustic cleaners are all tools that can help improve material flow.
Each of these has a specific purpose:
- Bin Activators: Help keep materials moving by vibrating the base of the silo or hopper.
- Screw Feeders: Control the flow of material, ensuring a consistent discharge rate.
- Pneumatic Vibrators: Agitate materials and prevent them from clumping together.
- Acoustic Cleaners: Use sound waves to loosen stuck materials, which is especially useful for fine powders.
Using these aids can turn a funnel flow system into a mass flow system, significantly reducing the chance of ratholing.
Consider Flow Properties in Design
Before building or selecting a storage structure, it’s important to test the flow properties of the materials you’ll store. Flow properties can influence whether a material will flow smoothly or become prone to ratholing. Testing these properties can help you determine the optimal hopper shape, slope, and outlet size.
Operational Techniques to Improve Material Flow
In addition to good design, adjusting your operational practices can help prevent ratholing. Here are a few practical tips:
- Use Flow Aids Strategically: Flow aids are effective, but they need to be used correctly. For example, installing a pneumatic vibrator too high on a silo wall might not reach material near the base, where ratholing is more likely to occur. Placing flow aids in the right locations ensures that material flows evenly and reduces the chance of stuck material.
- Adjust Fill and Discharge Rates: The speed at which you fill and empty a silo or hopper can impact flow patterns. Filling too quickly can cause materials to pack tightly, leading to flow issues like ratholing. Discharging material at a consistent rate can also help prevent the formation of rat holes.
- Monitor Changes in Material Behavior: Sometimes, changes in the materials you store can cause unexpected flow issues. If a new batch of raw material has a different moisture content or particle size, it may flow differently than usual. Monitoring these changes and adjusting your approach can prevent ratholing from catching you off guard.
Importance of Regular Maintenance and Inspections
Even with the best design, maintenance is essential to prevent ratholing over time. Regular cleanings and inspections can help you catch and address flow problems before they cause major disruptions.
The Role of Routine Cleaning
Cleaning your silos, hoppers, and bins regularly is crucial for preventing material buildup. Stuck material can cause a rat hole to form, which may worsen over time. This is especially important for materials prone to sticking, like fine powders.
Inspection for Flow Issues
Regular inspections can help identify potential flow problems early. For example, if you notice that material is only flowing through a small section of the hopper outlet, it could be a sign that a rat hole is forming. Addressing the problem at this stage prevents it from becoming a bigger issue that requires more intensive cleanouts or repairs.
Maintaining Flow Aids
Flow aids like screw feeders and pneumatic vibrators require occasional maintenance to ensure they remain effective. This might include checking for wear and tear or making sure they are properly calibrated to handle the specific material. Keeping these devices in good condition helps prevent disruptions in flow.
Partnering with the Pros for Long-Term Ratholing Prevention
Preventing ratholing is an ongoing process, requiring the right design, tools, and practices. But even with all these measures in place, there are times when professional help is needed. This is where partnering with a company like Silo Pros can be invaluable.
1. Why Professional Services Matter: We offer a deep understanding of how different materials behave in various storage structures. Our team’s expertise can help identify the best solutions for ratholing and other flow issues, whether it’s a minor adjustment or a more extensive redesign. Our services include thorough inspections, cleaning, maintenance, and repairs—ensuring that your silos, hoppers, and bins stay in optimal condition.
2. Tailored Solutions for Your Specific Needs: Every operation is unique. We provide customized solutions based on the type of material you handle, whether it’s bulk solids, fine powder, cement, or any other material. We recommend the best flow aids and help design or retrofit storage structures to achieve consistent mass flow, avoiding the hassle and cost of flow problems.
3. Long-Term Benefits: Investing in professional services for ratholing prevention can save time, reduce costs, and improve the efficiency of your operation in the long run. By preventing unexpected shutdowns and minimizing material waste, you’ll ensure that your process runs smoothly and efficiently.
Pro-Level Ratholing Maintenance and Prevention
Don’t let ratholing slow you down—take the steps today to ensure consistent flow and maximize your storage capacity.