Concrete plays a role in construction projects of all sizes, from building skyscrapers to setting a simple fence post. But to achieve high-quality concrete with the desired compressive strength, you have to consider the mixing process. Concrete batching and concrete mixing are both vital steps in creating concrete, yet they serve entirely different purposes.
What is Concrete Batching?
Concrete batching is the process of measuring and combining the main ingredients of concrete, including cement, sand, gravel, water, and any necessary additives or admixtures. This step ensures that the materials are measured in the right proportions, known as the mix design, to achieve the desired strength of concrete and performance.
Types of Concrete Batching
#1 Volume Batching:
- Materials are measured using containers like buckets or boxes.
- This method is simple but less accurate, often used for smaller construction projects like a deck footing or deck footer.
#2 Weight Batching:
- Materials are weighed using scales to ensure precise proportions.
- Commonly used in larger batch plants or central-mix batch plants to produce consistent high-strength concrete.
Why is Batching Important?
Proper batching ensures:
- The right cementitious materials to water ratio (also called the c ratio) for desired properties like compressive strength.
- Consistent results, avoiding weak spots or fast-setting concrete failures.
- Efficient use of materials, reducing waste in a concrete batch plant or mixing plants.
What is Concrete Mixing?
Once batching is complete, the next step is concrete mixing. This process combines the measured materials to create a uniform concrete mixture. Mixing ensures that every cubic yard of concrete has the same quality and properties.
Methods of Concrete Mixing
#1 Hand Mixing:
- Done manually for small-scale projects, like mixing mortar mix for a fence post.
- Often uses tools like shovels to blend sand, gravel, and cement.
#2 Machine Mixing:
- Involves a concrete mixer (also called a truck mixer) to blend materials thoroughly.
- Used in larger projects where high-quality concrete is required.
#3 Central Mixing:
- Happens at a central mix plant, where materials are mixed before being loaded onto a ready-mix truck.
- Produces a more consistent final product compared to dry mix systems.
Differences Between Batching and Mixing
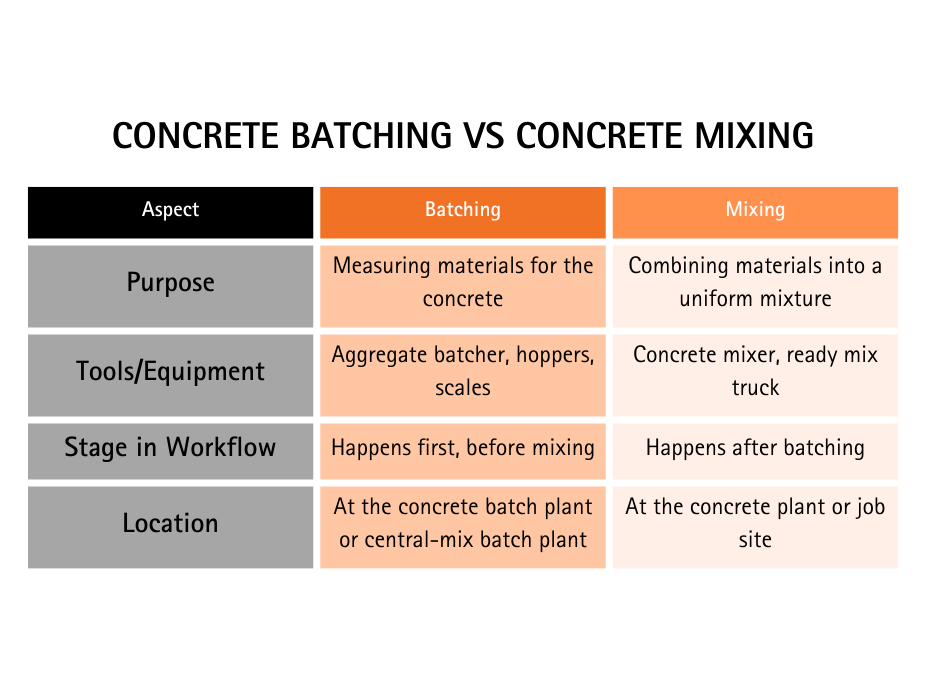
Challenges in Batching and Mixing
Challenges in Batching
Errors in measurement can occur when an aggregate batcher or scales are used improperly, leading to incorrect proportions of materials. Additionally, variations in ambient temperature can significantly impact the materials, altering the water content and setting times, which may compromise the quality of the concrete.
Challenges in Mixing
Overmixing can reduce the compressive strength of concrete by breaking down the aggregates, resulting in a weaker structure. On the other hand, undermixing can lead to an uneven concrete mix with pockets of cement, which weakens the final product and compromises its overall durability.
Best Practices for Concrete Mixing
- Follow Manufacturer Instructions: Always adhere to the recommended mixing plant settings and mix design ratios.
- Monitor Ambient Conditions: High or low ambient temperature can affect the water content and setting time of the concrete.
- Ensure Proper Equipment Maintenance: Regularly clean and maintain equipment like concrete silos, mixers, and batch plants to prevent contamination and ensure efficiency.
- Use a Central Mix Plant for Large Projects: For consistent, high-strength concrete, a central mix plant ensures uniformity in the final product.
Silo Pros: Expert Concrete Chipping Services
At Silo Pros, we specialize in concrete chipping services to keep your concrete silos and mixers in optimal condition. Our team removes hardened material safely and efficiently, ensuring that your silos operate at full capacity.
Benefits of Choosing Silo Pros:
- Reduces downtime at your batch plant or central-mix batch plant and restores 100% capacity
- Ensures compliance with standard permit requirements for silo maintenance.
- Restores the full capacity of stored materials, maximizing the efficiency an output of your equipment.
To keep your operations running smoothly, trust Silo Pros for expert silo cleaning and concrete chipping services.
Contact us today to learn how we can support your construction projects.